How to Remove FDM Support Material

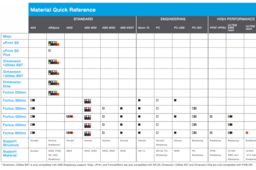
FDM (fused deposition modeling) Technology lets you 3D print parts in a broad range of well tested plastics. FDM materials offer specialized properties like toughness, electrostatic dissipation, translucence, biocompatibility, UV resistance, VO flammability and FST ratings. This makes them perfect for demanding designers and engineers in aerospace, automotive, manufacturing, medical and other industries.
-
Step 1: Materials Overview
Stratasys offers a diverse variety of model materials (see Table 1-2) which are used in conjunction with two types of FDM support materials. Soluble Release Support (SR) material can be washed away in a solution of heated-water and a cleaning agent, while Breakaway Support Structures (BASS) are manually removed. Notable differences between soluble support and BASS materials are as follows:
1.1 SR vs. BASS
Soluble Release (SR) support materials are very similar; however, they do offer some differences:
- SR-20 tends to discolor the support removal solution faster than SR-30
- SR-30 is less likely to shatter and dissolves 69% faster than SR-20
- SR-30 doesn’t expand as much as SR-20 in solution. Therefore, fragile parts won’t break from support expansion.
1.1.1 BASS Removal Tips
Warning: Always wear safety glasses and safety gloves when removing support material by hand. The support material can be brittle and may cause cuts when manually broken off.
Breakaway support structures (BASS) are removed manually, rather than by use of a tank containing a solution of heated-water and a cleaning agent. This method is ideal for parts build using simple support structures. Depending on the part built it may be difficult to reach all support structures in order to break them away, resulting in a greater amount of time spent removing supports. The following tips will help expedite the process of removing BASS.
1.1.2 Tools
The use of hand tools can greatly reduce the amount of time spent removing BASS from finished parts (suggested tools shown below). However, care should be taken to ensure that you do not scratch or gouge parts when using tools. For fragile parts, it is always best to take your time in order to eliminate the risk of damaging the part.
You may find that traditional tools are insufficient for removing supports from your parts. If so, you may need to fabricate custom tools to better suit your support removal needs.
1.1.3 Heat
ULTEM and PPSF support materials are much easier to remove if heated. (PC_S does not require re-heating as this material is generally easier to remove than ULTEM and PPSF supports). Placing a finished part into an industrial oven and allowing the part to heat will make support material easier to remove. However, if you decide to heat a part, do not place low temp parts (such as ABS-M30) into a high temp over (such as 160 degrees C). This can damage the part, possibly making it unusable. Please also keep in mind that the more heating/cooling cycles conducted, the more difficult it will be to remove supports. In general, materials should be heated to the temperatures specified in Table 1-3.
-
Step 2: WaterWorks Best Practices
2.1 WaterWorks Overview
WaterWorks in combination with Stratasys’ soluble support materials, dissolves soluble support structures with a water based solution (rather than requiring you to manually remove supports). See Table 1-2 for model and support compatibility information.
Stratasys software automatically creates any needed support structures to build specific parts. When applicable, WaterWorks provides the final step, enabling complex geometric and fully functional assemblies in single build.
Agitation aids in support removal; therefore, Stratasys recommends using either a circulation or ultrasonic tank.
WaterWorks concentrate comes in 1 liter bottles, which cannot be shipped by air. Each bottle treats 42 liters (11 gallons) of water.
2.2 Safety Guidelines
When using WaterWorks soluble concentrate and a support removal tank, observe the following safety guidelines:
- Follow the manufacturer’s documentation on tank operation and safety.
- Understand how to properly and safely use the tank before operation.
- Always wear safety goggles (indirectly vented and chemical splash resistant).
- Use rubber gloves that can withstand the high solution temperature and high alkaline solutions. (Gloves that are cuffed at the elbow are recommended).
- Follow your company and local regulatory statutes regarding safety practices.
- Never place hands in a tank filled with solution and/or hot water.
- Always use a proper tool to remove parts from the tank. Plastic or stainless steel removal tools are recommended that can withstand the high solution temperature and high alkaline solution in the tank.
- If using a basket, remove the entire basket from the tank before removing parts.
2.3 Choosing a Support Removal
A variety of support removal tanks can be utilized to aid in the process of removing support materials from finished parts. Tank options vary depending on whether you’re using a circulation or ultrasonic tank. Agitation aids in support material removal; Stratasys recommends using either a circulation or ultrasonic tank. The tank must be able to withstand various water temperatures (see Table 2-1 below for details) and high alkaline solutions with a pH up to 12.6.
Parts can be secured in the tank using stainless steel, porous baskets or other containers, which lessens the chances of parts being damaged. A stainless steel tea infusing ball (3 inches), or similar container, works well for small parts. Larger parts with fine feature details can be secured to a basket with plastic cables ties.
2.3.1 Circulation Tanks
- Uses heat and circulation.
- Circulation amount and strength varies for each tank.
- Generally used with lids, and therefore has less evaporation than ultrasonic tanks.
- Quieter than ultrasonic tanks.
- Secured parts may need to be checked periodically to ensure that they are fully submerged/stay submerged in the tank.
2.3.2 Ultrasonic Tanks
- Uses heat and sound waves to create scrubbing bubbles, which gently clean parts.
- Generally not used with lids to avoid overheating.
- WARNING: Bath solution will have a high pH, use caution to avoid contact with skin.
- Louder than circulation tanks.
- Best for small or fragile parts with fine features, and parts with thin channels or small holes.
2.4 Recommended WaterWorks Compatible Tanks
The following third-party support removal tanks are recommended for use by Stratasys. As this list is subject to change, always see your Regional Sales Representative for recommendations. Stratasys does not manufacture, sell, or service these tanks.
2.4.1 Omegasonics
Two omegasonics Ultrasoinc Parts Washers are available for use with WaterWorks solution.
Omegasonics 1900 BT
The Omegasonics 1900 BT is a 28 gallon (106 liters) capacity tank. Typical water level height is 6 inches (15.2 cm) from the top of the tank lip, which provides 20 fluid gallons (75.7 liters); therefore, two bottles of WaterWorks should be used to charge the tank.
- Overall dimensions: 28.75 in. (73 cm) wide x 22 in. (55.9) deep* x 27 in. (68.7 cm) high *add 3.5 in. (8.9 cm) for drain.
- Electrical requirements: 1 Phase / 120 VAC / 15 Amp.
- Power cord location: 7 in. (17.8 cm) from back left corner, 4 in. (10.2 cm) from ground.
- Plumbing: 1 in. (2.54 cm) drain valve location 3.75 in. (9.52 cm) from back right corner, 5.5 in. (14 cm) from ground.
Omegasonics SST4030
The Omegasonics SST4030 is a 207 gallon (783.5 liters) capacity tank. Typical water level height is 8 inches (20.3 cm) from the top of the tank lip, which provides 175 fluid gallons (662.45 liters); therefore, 16 bottles of WaterWorks should be used to charge the tank.
- Overall dimensions: 64.75 in. (164 cm) wide x 33.75 in. (90.8 cm) deep x 54.25 in. (138 cm) high* *add 22.25 in. (56.5 cm) with doors open.
- Electrical requirements: 3 Phase / 240 VAC / 50 Amp.
- Power cord location: 11 in. (27.9 cm) from back left corner, 4 in. (10.2 cm) from ground.
- Plumbing: 1.5 in. (3.81 cm) drain valve location 7 in. (17.8 cm) from right corner, 8 in. (20.3 cm) from ground (left side of machine).
CleanStation XL Plus
The CleanStation XL Plus is the largest regular production CleanStation available. This part cleaning system is designed to remove WaterWorks soluble support material from finished parts, using jet action cleaning. Refer to the CleanStation XL Plus User Guide, available from the Stratasys Resource Center website, for more information.
The XL Plus features a 100 gallon (378.5 liters) capacity tank. Typical water level height is 3 inches (7.62 cm) from the top of the tank. 9 bottles of WaterWorks should be added into the tank; most will dissolve in 3 to 5 minutes
- Work envelope dimensions: 25 in. (63.5 cm) x 37 in. (94 cm) deep x 25 in. (63.5 cm) high
- Electrical requirements: 3 Phase / 240 VAC / 70 Amp. 51FLA, 3 wire with a ground and no neutral.
- Power cord location: Facing the rear of the machine, the power cord connection is located at the middle right of the unit.
- Plumbing: Facing the rear of the machine, the drain is located at the left rear of the unit.
The CleanStation SRS II
The CleanStation SRS II is a heavy-duty, professional-grade support removal system designed to remove WaterWorks soluble support material from finished parts, using jet action cleaning. To protect delicate parts, the system is equipped with active cooling to prevent warping and de-lamination due to overheating. The SRS II is also available with a variable flow option which allows operators to control jet flow rates.
The SRS II features a 17 gallon (64.35 liters) capacity tank. There is a low level cut-off switch approximately 4 in. (10.2 cm) from the top of the tank; the machine will not operate if the solution level falls below this switch. One and a half (1.5) bottles of WaterWorks should be added into the tank once water temperature reaches 150° F (65.6° C); most will dissolve in 3 to 5 minutes.
- Work envelope dimensions: 16 in. (40.6 cm) x 14 in. (35.6 cm) deep x 16 in. (40.6 cm) high
- Electrical requirements: 1 Phase / 240 VAC / 20 Amp
- Power cord location: Facing the rear of the machine, the power cord connection is located at the lower right of the unit.
- Plumbing: Quick disconnect, appliance style plumbing.
SCA - 1200
The SCA (support cleaning apparatus)-1200 can be used in conjunction with any support removal concentrate (WaterWorks or Ecoworks packets) in order to remove soluble support material from finished parts. The SCA-1200 uses an optimized nozzle which circulates the heated cleaning solution in and around parts to dissolve away soluble support material.
The SCA-1200 features an 8.3 gallon (31.5 liter) tank which is ideal for removing support material from large parts. 850 grams (roughly 4/5 of a bottle) of WaterWorks should be added to the tank.
- Physical dimensions: 16 in. (40.6 c,) x 19 in. (48.3 cm) x 26.5 in. (67.3 cm).
- Basket capacity: 10 in. (25.4 cm) 10 in. (25.4 cm) x 12 in. (30.5 cm).
- Electrical requirements: 100-120V ~ 60Hz 15A.
2.5 Removing Support Material
Some parts have support materials that are hard to remove (e.g., parts with thin, deep channels), resulting in longer dissolving times. While some parts have support material that cannot be removed (e.g., hollow parts with non-accessible interiors). Therefore, it is suggested but not required that you remove some support by hand in order to save tank time and water life span, except when using SR-100. When using SR-100 it is required that you manually remove small amounts of support material prior to placing parts in the tank. This will help eliminate any likelihood of part breakage while in the tank. Thin-walled or small feature part geometries (less than or equal to 0.02 in. (0.50 mm)) with encapsulated regions of support may be susceptible to breakage or cracking. This is due to slightly faster thermal expansion of the SR-100 soluble support material compared to the thermal properties of the polycarbonate (PC) model material.
2.5.1 Adding Solution to the Tank
To begin, fill the tank with water.
- The ratio of water needed is 11 gallons (42 liters) of water per one bottle (2.1 lbs/950g) of soluble concentrate
Make sure to fill the tank according to the operating instructions set by the manufacturer to avoid burning out the tank’s heater (or transducer in ultrasonic units).
Carefully open one bottle of soluble concentrate (per 11 gallons of water) and slowly spread the powder over the entire water surface in the tank.
When finished, seal and store bottles with remaining concentrate. Dispose of empty bottles appropriately.
Over time evaporation can occur; periodically check for evaporation of water. If evaporation occurs add more water, do not add more soluble concentrate.
2.5.2 Tank Temperature
Always power the tank ON according to the operating instructions set by the manufacturer. When dissolving support material, set the tank’s temperature according to the information listed in Table 2-1. Verify that the tank’s temperature configuration is correct for the type of support material being removed before placing parts in the tank. Always allow the solution to reach proper temperature before placing parts into the solution. Support material dissolves the fastest at the designated support material temperature. Filling the tank with hot tap water will help accelerate the time needed to reach designated operating temperatures.
2.5.3 Placing Parts in the Tank
Follow the operating instructions set by the tank manufacturer as to where parts can be placed within the tank (e.g., free moving or secured in a basket or other porous container). In some tanks, for example, parts cannot be placed on the bottom. Multiple parts may be placed in the tank but there must be sufficient room within this tank to allow for adequate agitation.
Enclosures should be used to ensure that fragile parts are not damaged while in the tank. Always keep parts fully submerged within the tank’s solution; if parts do not stay fully submerged grime can build-up on the part’s surface. Sparse filled parts will absorb solution; therefore, adding holes for draining is advised. Sparse filled parts will float within the tank’s solution so they should be anchored within the basket or tank to ensure they stay fully submerged.
2.5.4 Material Specific Guidelines
PC Material
PC parts left in a tank for excessive time may see a 5-15% drop in mechanical properties. It is good practice to allow PC parts to soak in the tank for 4 hours, and then check parts frequently to ensure that they are not left in the tank for too long.
Nylon 12 Material
Nylon 12 may be brittle out of the oven. A very specific process should be followed when placing Nylon 12 parts into a tank containing WaterWorks solution.
- After removing a Nylon 12 part from the printer’s oven, always leave the part on the build sheet. Allow the part to cool on the build sheet until it is room temperature.
- Carefully pull the part off of the build sheet once it is room temperature. The part may be fragile so care must be taken.
All Nylon 12 parts must be placed into a WaterWorks solution bath; a minimum of 4 hours of re-hydration is suggested.
2.5.5 Inspecting Parts and Solution
Support material can be washed away from part geometries in 0.5 to 3.0 hours, given the support removal tank’s solution maintains proper temperature and pH levels. Various factors determine how long it takes to remove support material in the tank. To ensure timely and efficient support removal:
- Minimize the volume of support material on the part prior to placing it into the tank.
- Minimize the amount of time parts spend in the solution tank.
- Minimize the amount of dissolved solids in the solution tank.
- Maximize the pH level in the solution tank.
- Maximize solution agitation around parts.
For best part quality, inspect parts after 2 hours and then periodically until their clean cycle is complete.
Due to air pockets and circulation patterns it is recommended that you rotate the basket or free moving parts to dissolve support material faster. Inspect the tank periodically for overheating and solution evaporation. The solution level must always cover the parts. Add more water if necessary; do not add more soluble concentrate.
2.5.6 Removing Parts from the Tank
To begin, turn OFF power to the tank. Allow the tank’s cover to drip for a few moments before removing the lid completely. Carefully remove parts from the tank; plastic or stainless steel removal tools (such as tongs) are recommended for removing parts. Removal tools need to be able to withstand high water temperature and high alkaline solution.
Parts must be rinsed after they’re removed from the tank, rinse parts as follows:
- White Parts: Rinse parts thoroughly with water until part surfaces are no longer slippery (1-2 minutes). To reduce the possibility of staining, some white parts may need to soak for an hour to help pull soluble concentrate from part surfaces. Also, soaking parts in a dishwasher rinsing aid and water and then rinsing the parts will break the surface tension.
- Color Parts: Soak parts in water for one hour to dissolve and pull soluble concentrate from part surfaces. Also, soaking parts in a dishwasher rinsing aid and water and then rinsing the parts will break the surface tension.
- Soft Water or Deionized Water: Sparse parts need to be drained and re-rinsed. A vacuum chamber can be used to pull solution out of the part.
For parts built using the sparse build style, allow parts to drain fully as solution can get trapped inside the part. Allow parts to dry thoroughly and then rinse parts (for 1-2 minutes) under hot water, once again making sure that you do not allow any water to get trapped inside the part.
Dry parts with paper towels, compressed air, or let them air-dry. If colored parts turn slightly white after drying, rinse them under hot water or soak them again as previously instructed.
2.5.7 Changing Solution in the Tank
How often the solution is changed is dependent on the tank used, how it is maintained, and the complexities of the parts built. Stratasys recommends changing a tank’s solution after it has been used to remove approximately 25 cubic inches (410 cc) of support material (~ 2lbs/ 9kg) per 11 gallon (42 liter) tank, or the pH falls to 11.5. The following conditions indicate that the solution should be changed:
- The tank begins to cloud or exhibit low clarity. Some white parts (ABS) may turn brown or yellow.
- Parts have a sticky residue and/or stick together in the tank due to excess dissolved solids in the tank.
- Functional parts with moving features are not functioning properly.
- Support material is not fully removed after a long cleaning cycle.
- The tank’s solution exhibits a low pH (this can be determined by checking pH level using a test strip or meter).
2.5.8 Disposing of Soluble Concentrate
The soluble solution has been specially formulated to be safely disposed after dilution and neutralization to an acceptable pH level. The pH level of fresh solution is similar to that of typical laundry detergents, dishwasher detergents, and common household cleaners.
2.5.9 Soluble Solution Drain Effluent
Dilute the solution with water using the appropriate ratio to meet acceptable pH levels. The Drain Effluent data below is based on a dilution of 1 part soluble concentrate to 5 parts water containing approximately 28 cubic inches (459 cc) of soluble release material dissolved in 11 gallons (42 liters) of water, resulting in a pH of 11.8.
2.5.10 Neutralization
The soluble solution can be further neutralized to lower the pH level by slowly adding acid (e.g., malic acid) to the tank before draining the solution.
To successfully neutralize a solution of soluble concentrate dissolved in 11 gallons (42 liters) of water to a pH level below 11:
- Check local codes. Refer to the MSDS sheets for proper safety precautions and possible hazards for malic acid.
- Slowly add 14 ounces (397 grams) of malic acid to the tank solution (this amount is based on starting pH level); pH will reduce from 11 to 8. Please note that the tank will foam.
2.5.11 Tank Cleaning
In the event your tank needs to be returned to the manufacturer for service repair, you may be required to thoroughly clean the tank to remove all concentrate residue prior to shipment.
To clean the tank:
- Drain, dilute, and/or neutralize the tank solution.
- Re-flll the tank with clean tap water and operate a few minutes to circulate clean tap water throughout the system.
- Drain the tank and wipe down all surfaces to remove traces of the soluble concentrate.
-
Step 3: Ecoworks Best Practices
3.1 Ecoworks Overview
Ecoworks cleaning agent is designed to remove SR-30 support material from parts built using the FDM process with soluble support material. See Table 1-1 and Table 1-2 for model and support compatibility information. The cleaning agent is both user- and eco-friendly (with a pH of 10). Ecoworks comes in tablet or packet form and usage varies by tank type.
No personal protection equipment is required when handling the cleaning agent and disposal of the used solution requires only dilution with clean water to meet generally acceptable world-wide disposal standards.
This step details the recommended guidelines for using Ecoworks. Refer to the Ecoworks User Guide, available from the Stratasys Resource Center website, for more information.
3.2 Safety Guidelines
When using Ecoworks and a support cleaning system observe the following safety guidelines:
- Follow the manufacturer’s operation and safety documentation. Understand how to properly and safely use the cleaning system before operation.
- Follow your company and local regulatory statutes regarding safety practices.
- Make sure the appropriate voltage range for your region has been selected. Avoid overloading the electrical outlet with multiple devices
- Prior to operation, ensure that the system is on a flat and stable surface that is capable of supporting the system’s weight.
- Ensure the system is well-grounded. Failure to ground the system may result in electrical shock, fire and susceptibility to electromagnetic interference.
- Use only the power cord supplied. Do not damage, cut or repair the power cord. A damaged power cord has risk of fire and electric shock. Replace a damaged power cord with an approved power cord.
- Do not allow metal or liquids to touch the internal parts of the system. Doing so may cause damage, fire, electric shock or other serious hazards.
3.3 Recommended Ecoworks Compatible Tanks
The following cleaning systems are recommended for use by Stratasys. As this list is subject to change, always see your Regional Sales Representative for recommendations. Stratasys manufactures, sells, and services the WaveWash and WaveWash 55 systems.
3.3.1 WaveWash / WaveWash 55 Overview
The WaveWash and WaveWash55 Support Cleaning Systems are specifically developed to provide efficient removal of SR-30 soluble support material from parts built using the FDM process. These systems remove support material by immersing finished parts in a bath of water with a specific amount of cleaning agent (in either tablet or packet form) added to the cleaning agent receptacle. The system heats and circulates solution around the parts in the cleaning tank.
The solution dissolves the support material without harming the underlying model material. Over time, depending on geometry and the amount of support material, all the support material is dissolved and the parts are ready to be removed, dried and used for their intended purpose. Refer to the WaveWash User Guide/WaveWash 55 User Guide, available from the Stratasys Resource Center website, for more information.
3.3.2 WaveWash
The WaveWash Support Cleaning System comes in the uPrint SE and uPrint SE Plus 3D Print Packs, and is also sold separately. This system is designed to wash away support materials, rinse parts, and drain automatically.
The WaveWash system is used in conjunction with Ecoworks packets. These packets consist of two pre-measured dissolvable pouches (labeled A and B) which are placed into the WaveWash tank. Once exposed to water within the tank, these packets mix together to form the solution used to remove support material. One set of packets treats one WaveWash tank, or 3.6 gallons (13.5 liters) of water.
Dimensions 17.25 in (43.8 cm) x 18.24 (48.33 cm) x 17 in. (43.18 cm).
Basket capacity: 8 in. (20.3 cm) x 8 in. (20.3 cm) x 6 in. (15.2 cm).
Electrical requirements: 100-120 VAC / 50/60Hz / 1200W.
Plumbing: Incoming water source and drain connection required.
3.3.3 WaveWash 55
The WaveWash 55 Support Cleaning System comes in the Mojo 3D Print Pack, and is also sold separately. This system automatically turns off heating and agitation at the end of a cleaning cycle.
The WaveWash 55 system is used in conjunction with Ecoworks tablets. One tablet will treat a WaveWash 55 carafe, or up to 1.3 gallons (5 liters) of water.
Dimensions: 13.2 in. (33.5 cm) x 13.2 in. (33.5 cm) x 13.2 in. (33.5 cm).
Basket capacity: 5 in. (12.7 cm) x 5 in. (12.7 cm) x 5 in. (12.7 cm).
Electrical requirements: 100-120 VAC / 6 Amp / 60Hz or 220- 240 VAC / 2.5A / 50Hz
Plumbing: No plumbing required.
3.3.4 SCA-120
The SCA (support cleaning apparatus)-1200 can be used in conjunction with any support removal concentrate (Ecoworks packets or WaterWorks) in order to remove soluble support material from finished parts. Stratasys does not manufacture, sell, or service this system.
The SCA-1200 uses an optimized nozzle which circulates the heated cleaning solution in and around parts to dissolve away soluble support material.
The SCA-1200 features an 8.3 gallon (31.5 liter) tank which is ideal for removing support material from large parts. When using Ecoworks, the entire contents from 4 packets (2 A packets and 2 B packets) should be added to the tank.
Physical dimensions: 16 in. (40.6 cm) x 19 in. (48.3 cm) x 26.5 in. (67.3 cm).
Basket capacity: 10 in. (25.4 cm) 10 in. (25.4 cm) x 12 in. (30.5 cm).
Electrical requirements: 100-120V~ 60Hz 15A.
3.3.5 Ecoworks Packets & WaveWash
Ecoworks packets are used in conjunction with the WaveWash Support Cleaning System, and provide efficient removal of SR-30 soluble support material. Each packet consists of two pre-measured dissolvable pouches (labeled A and B) which are placed into the WaveWash tank.
The system removes support material by immersing parts in a bath of water with a specific number of Ecoworks packets added to the clean tank. The system heats and circulates solution around the parts in the cleaning tank. The solution dissolves the support material without harming the underlying model material. Over time, depending on geometry and the amount of support material, all the support material is dissolved and the parts are ready to be removed, dried and used for their intended purpose.
3.3.6 Tank Level and Ecoworks Amounts
The WaveWash system allows for a user-selectable clean tank level. A full clean tank level is approximately 4 gallons (15.14 liters) of water, while a half clean tank level is approximately 2 gallons (7.57 liters) of water. The system will automatically fill with water based on the selected clean tank level.
- One Ecoworks packet (one A and one B pouch) should be used for a half clean tank level. The entire contents of the package should be used.
- Two Ecoworks packets (two A and two B pouches) should be used for a full clean tank level. The entire contents of each package should be used.
As general practice to optimize support removal and meet generally acceptable pH levels for waste water disposal, one packet of Ecoworks should be used for every 2 gallons (7.5 liters) of water. For each additional two gallons (7.5 liters) of water, add an additional packet of Ecoworks. For example, an 8 gallon (30 liter) tank requires 4 packets of Ecoworks. With the above ratio of Ecoworks and water, the pH level of clean solution will be approximately 9.8.
3.3.7 Clean Cycle
The WaveWash system allows for 3 user-selectable clean cycle lengths (Short, Medium, and Long). Factors such as model geometry, small support filled crevices, small blind holes, support styles other than SMART, or low water temperature coming into the system can impact the length of time required to clean parts. Table 3-1 should be used as a general guideline for selecting cycle lengths for most parts.
After the clean cycle is complete, the system drains and then refills with clean water for a final rinse and drain cycle. Once finished, the lid will unlock and parts can be removed. Allow the solution to drain off of the parts for a few minutes before removing them. Wash off any remaining solution and dry parts with a clean cloth or paper towel. Repeat the clean cycle if needed.
3.3.8 Temperature
The WaveWash system automatically sets and maintains water temperature within the clean tank. However, water temperatures between 70 - 75° C (158 - 167° F) are most effective for dissolving support materials. Temperatures above 75° C (167° F) may cause parts to distort. Dissolve times with temperatures below 70° C (158° F) will take longer
3.3.9 Solution Life and Disposal
How often you change the solution is dependent on the tank you use, how you maintain it, and the complexity of your parts. As support materials are dissolved over time, the pH level will decrease and dissolve times will increase. For optimal effectiveness, the solution should be changed after 1.5 lbs. (0.68 kg) or approximately 40 cu. in. (655 cu. cm) of support material has been dissolved. If you suspect that the solution’s pH is low, test the solution using a test strip or meter.
A Waste Water Profile is available for SR-30 soluble support material. This profile is based on the dilution of used solution with an equal amount of freshwater. For example, when disposing of 4 gallons (15 liters) of used solution, dilute with 4 gallons (15 liters) of fresh water. Check your local, state, and/or international regulatory statutes for what pH level is acceptable for disposal. The WaveWash system utilizes an automatic water drain feature; therefore, it is imperative that the correct ratio of Ecoworks packets to water be maintained when operating the system.
Stratasys recommends that disposal procedures be verified by the proper authorities in your region. Stratasys cannot anticipate local, state, or international regulatory statutes. Stratasys cannot be held liable if the solution is not handled and disposed of properly. You may need to document how you dispose of the used solution.
3.4 Ecoworks Tablets & WaveWash 55
Ecoworks tablets are used in conjunction with the WaveWash 55 Support Cleaning System, and provide efficient removal of SR-30 soluble support material. The system is environmentally friendly, allowing for municipal sewage disposal of used solution. The system removes support material by immersing parts in a bath of water with a specific number of Ecoworks tablets. The system heats and circulates solution around the parts in the carafe. The solution dissolves the support material without harming the underlying part material. Cleaned parts should be air dried before being used for their intended purpose.
3.4.1 Ecoworks Amounts and Water Level
One Ecoworks tablet should be added to the carafe before any water is added to the carafe. One tablet will treat one carafe, or up to 1.3 gallons (5 liters) of water.
Once the tablet has been added to the carafe, carefully place part(s) with soluble supports in the bottom of the carafe. All parts must be free to agitate in the cleaning solution. Do not overload the carafe with parts.
Manually fill the carafe with hot water. Always use hot water when filling the carafe; this will help dissolve the support structures more quickly. Fill the carafe so the water level is at least 3 in. (7.62 cm) above the part(s) or a maximum of 1 inch (2.54 cm) from the top of the carafe, whichever is less. Part(s) must be fully submerged during the cleaning process.
3.4.2 Clean Cycle
The WaveWash 55 system features a user initiated 8 hour automated clean cycle. Before starting a clean cycle ensure that the lid is on the carafe and the carafe is securely seated on its base. Once the clean cycle is complete, parts must be manually rinsed with hot water.
To rinse parts following a clean cycle, empty the Ecoworks solution from the carafe into a drain ensuring that parts remain in the carafe. Remove the lid and manually fill the carafe with hot water. Parts should be fully submerged. Allow parts to soak for approximately 5 minutes before emptying the water from the carafe. Allow water to drain off of the parts for a few minutes before removing them the carafe. Wash off any remaining residue with warm water and then dry parts with a clean cloth or paper towel. Repeat the clean cycle if needed.
3.4.3 Temperature
The WaveWash 55 System automatically sets and maintains water temperature within the clean tank. However, water temperatures between 70 - 75° C (158 - 167° F) are most effective for dissolving support materials. Temperatures above 75° C (167° F) may cause parts to distort. Dissolve times with temperatures below 70° C (158° F) will take longer.
3.4.4 Solution Life and Disposal
How often you change the solution is dependent on the tank you use, how you maintain it, and the complexity of your parts. As support materials are dissolved over time, the pH level will decrease and dissolve times will increase. For optimal effectiveness, the solution should be changed after 1.5 lbs. (0.68 kg) or approximately 40 cu. in. (655 cu. cm) of support material has been dissolved. If you suspect that the solution’s pH is low, test the solution using a test strip or meter.
A Waste Water Profile is available for SR-30 soluble support material. This profile is based on the dilution of used solution with an equal amount of freshwater. For example, when disposing of 4 gallons (15 liters) of used solution, dilute with 4 gallons (15 liters) of fresh water. Check your local, state, and/or international regulatory statutes for what pH level is acceptable for disposal. The contents of the WaveWash 55 carafe are intended to be emptied into a drain for disposal; therefore, it is imperative that the correct ratio of Ecoworks tablets to water be maintained when operating the system.
Stratasys recommends that disposal procedures be verified by the proper authorities in your region. Stratasys cannot anticipate local, state, or international regulatory statutes. Stratasys cannot be held liable if the solution is not handled and disposed of properly. You may need to document how you dispose of the used solution.
-
Step 4: Appendix A: Quick Reference & Tips
4.1 Material Reheating Temperatures
4.2 Ecoworks Quick Reference
The Ecoworks cleaning agent is designed to remove SR-30 support material from parts built using the FDM process with soluble support material. The WaveWash and WaveWash55 Support Cleaning Systems are designed to remove SR-30 support material using Ecoworks.
4.3 WaveWash & Ecoworks Ratio
The WaveWash Support Cleaning System comes in the uPrint SE and uPrint SE Plus 3D Print Packs, and is also sold separately. This cleaning system is used in conjunction with Ecoworks packets. These packets consist of two pre-measured dissolvable pouches (labeled A and B) which are placed into the WaveWash tank. One set of packets treats one WaveWash tank, or 3.6 gallons (13.5 liters) of water.
4.4 WaveWash 55 & Ecoworks Ratio
The WaveWash 55 Support Cleaning System comes in the Mojo 3D Print Pack, and is also sold separately. The WaveWash 55 system is used in conjunction with Ecoworks tablets. One tablet will treat a WaveWash 55 carafe, or up to 1.3 gallons (5 liters) of water.