Topology Optimization of Triangular Bracket - ANSYS Workbench

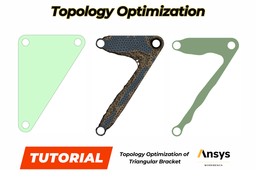
Topology optimization is a mathematical method which spatially optimizes the distribution of material within a defined domain, by fulfilling given constraints previously established and minimizing a predefined cost function. Main aim of this tutorial is optimizing and decreasing the material density of the triangular bracket as 50% by topology optimization.
-
Step 1: Overview
-
Step 2: Analysis Procedure
- As a very first step, the triangular bracket has been analyzed to obtain the maximum deformation, maximum stress (point of interest) and minimum safety factor.
- As the 2nd step, structural (topology) optimization analysis has been implemented to decrease the material density.
- As the last step, the optimized geometry has been reworked on SpaceClaim and analyzed once more.
-
Step 3: Engineering Data (Material Model)
- The default material which is Structural Steel have been used in this tutorial:
-
Step 4: Geometry (SpaceClaim Model)
- The triangular bracket has been designed on SpaceClaim could be seen below:
-
Step 5: Meshing Operations (Default Geometry)
- The default mesh with 0.6mm of Element Size has been created:
- The mesh refinement on point of interest (the area which has the maximum stress) has been refined until the stress value difference between two adjacent nodes is less than 10%.
- The first refinement on point of interest have been implemented as Body Sizing / Sphere of Influence with 1.5mm of Sphere Radius and 0.11mm of Element Size:
- The second refinement has been implemented as Inflation with 3 Layers and 1e-002mm:
-
Step 6: Boundary Conditions (Default Geometry)
- The Boundary Conditions have been implemented as below figure:
- Cylindrical Support has been implemented on 2 Faces with Free Tangential option:
- The Bearing Load has been implemented as seen below:
-
Step 7: Results (Default Geometry)
- Total Deformation:
- Equivalent (von-Mises) Stress:
- Minimum Safety Factor:
-
Step 8: Topology (Structural) Optimization
- Firstly, the engineering data, the geometry, the model and the results from Static Structural must be connected with Structural Optimization Analysis:
- Analysis Setting of Structural Optimization could be seen below:
- The Exclusion Regions (bearing load and cylindrical support areas) and Topology Region could be seen below:
- Material Density (Response Constraint) Reduction with 50% Mass has been determined:
- The result of the Topology Optimization could be seen below:
-
Step 9: The Geometrical Optimization of Resulted Geometry
- The resulted geometry from Topology Optimization results have been optimized according to new geometry boundaries:
-
Step 10: Results (Optimized Geometry)
- The analysis results for optimized geometry with the same boundary conditions could be found below.
- Total Deformation:
- Equivalent (von-Mises) Stress:
- Minimum Safety Factor: